一个恰当的例证是M5C90,一款创新刀具 — 一款刀具兼具粗加工和半精加工两种能力。M5C90是一款定制型高速面铣刀具,旨在为客户彻底消除费时的调试操作。M5C90的每齿数量少于传统刀具,主要得益于其最后一排/内直径上专门的径向和轴向刀片定位 (无需调整刀片)。这种定位保证了铣削无毛刺以及出色的表面质量,包括气缸盖、气缸体、制动系统零件以及所有可实现大切宽的铝合金零件 (不适用于薄壁零件)。
为了举个例子说明使用M5C90可能获得的益处,可考虑持续在客户处进行个案试验,试验对象为AlSi12Cu1材质的制动系统主体阀门。所用刀具的外直径配备10个硬质合金刀片,内直径配备四个刀片 (外加一个Wiper (修光刃) 刀片),主轴转速8000 rpm,切削速度4021 m/min (13,192英尺/分钟),进给率0.25 mm/齿 (0.009英寸齿)。此外,轴向切深2 mm (0.078英寸),径向切深140 mm (5.51英寸),金属去除率5600 cm3/min (342立方英寸/分钟)。虽然刀具的寿命到底如何还有待检验,但是已知的一个事实是:同样款式的刀具在工作了18个月后至今仍留在机床内继续效力。
如果需要一款还能对薄壁铝合金件 (例如齿轮箱壳体和箱体件) 进行精加工的刀具,山特维克可乐满还有另外一款同样高效的刀具可供选择,即:M5F90。M5F90是又一款只需一道工序即可完成粗加工和精加工两种加工的便捷刀具。刀体直径25-80 mm (0.98-3.15英寸),配备焊接PCD刀尖,专用于薄壁铝合金件的加工以及点铣和面铣工序。每一个刀尖都配有粗加工和精加工两种切削刃。粗加工区域作为传统铣削刀具使用,所有切削刃均为一致的直径和高度;而精加工区域由径向轴向步进式切削刃构成。这种概念促成了密齿距,从能够实现无毛刺的加工和出色的表面质量。
另外也大幅节省了时间,这一点从某个客户个案试验就可看出,即:对铝合金 (Si含量高) 气缸盖进行面铣加工。在这个案例中,相比竞争对手的一款特制PCD刀具,M5F90不仅使生产周期缩短了150%,而且彻底避免了毛刺的生成。切削参数:主轴转速15,915 rpm;切削速度2000 m/min (6562英尺/分钟);进给率0.16 mm/齿 (0.006英寸/齿);切削深度1.5 mm (0.06英寸)。
还有一个关于M5F90的实例,是关于铝质链条盒的生产:相比竞争对手的63 mm (2.48英寸) 直径可转位刀具 (配有六个PCD刀片),M5F90的生产周期缩短了44%。此外,得益于该方案,之前必不可少的去毛刺工序再无用武之地。
另外一个新款非标刀具是M610,用于双金属接面发动机气缸体顶面的铣削加工,通常是铝合金和灰口铸铁 (CGI) 这两种金属。
一系列热特性和机械特性使双金属材料的加工充满挑战。现有用于该应用的铣削刀具复杂且需要调节,因此使生产率打了折扣。此外,该类刀具还经常在零件的GCI部位发生崩刃。
而M610完全相反,它无需装夹,也无需调整,在采用高进给率时也不会导致崩刃,也不会使零件产生毛刺或刮痕。这种能力非常重要,因为表面瑕疵有可能导致气缸体和气缸盖之间产生泄漏,进而有损功率和性能。一些全球性的汽车OEM已经因为采用了M610而受益匪浅。
以其中一个客户为例,其在双金属发动机体的燃烧工作面精加工方面赢得了巨大的竞争优势。同竞争对手的一款配有刀卡的可调刀具相比,M610的刀具寿命提升了833%之多,加工零件数量超过4000件,而竞争对手的刀具只加工了480件。而且,M610的速度快9倍。配有15个刀片的M610的切削参数如下:切削速度3000 m/min (9843英尺/分钟);进给速度5720 mm/min (225英寸/分钟);主轴转速3820 rpm;进给率0.15 mm/齿 (0.006英寸/齿);加工铝合金的切削深度0.5 mm (0.02英寸),加工铸铁的切削深度0.05 mm (0.002英寸)。
该系列的其他刀具包括M5Q90切向粗加工刀具,只需一道工序即可完成第一阶段的毛坯加工 (铸造之后初次进行的表面加工),没有毛刺。该刀具配备PCD切向刀片,可实现顺畅而稳定的切削作用,从而降低功率消耗并消除振动。
铝合金气缸盖和气缸体就是M5Q90刀具的受益零件之一。举例来说,缸盖的铸造毛坯加工工序一般包括轴承面加工、进/排气面加工和燃烧室面加工。在某个客户案例研究中发现:通过卧式机床中心对AS-9铝合金气缸盖铸造件进行面铣粗加工,刀具寿命表现相当出色。切削速度3000 m/min (9843英寸/分钟),每齿进给0.2 mm (0.008英寸),轴向切削深度2.0 mm (0.079英寸) (完全吃刀达到40 mm (1.57英寸),最后产出零件超过10,000件。
另外还有一款刀具是M5R90,用于第二阶段的粗加工/半精加工。这款标准刀具采用可调刀卡,能够以0.4或0.8 mm (0.016或0.031英寸) 的半径实现最大8 mm (0.315英寸) 的切深,具体取决于所用的刀卡。易于调节的刀卡有益于很多汽车应用,最近一个客户的试用就体现了这种益处:主要是对发动机盖进行面铣加工。比起在市场上占据大份额的竞争对手的刀具产品,以MRHB Si12铝合金材质铸造而成的M5R90表现相当出色。在各项切削参数完全一致的前提下,M5R90将刀具寿命从8000个工件提升到10,000个。此外,由于刀卡移动,竞争对手的刀具在每加工1000个零件后需要调整一次,这样有损表面质量。而与此形成鲜明对比的是,M5R90在需要进行任何调节前能够坚持加工出8000个零件。
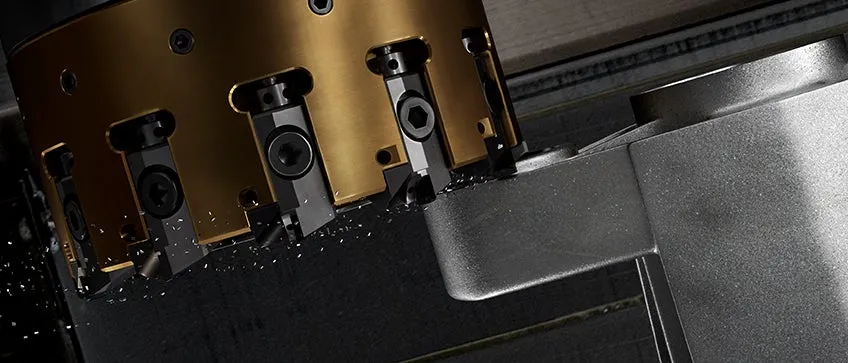
该系列还包括M5B90超级精加工面铣刀具,刀片拥有专门的轴向和径向位置。这种配置,加之Wiper (修光刃) 刀片,确保了出色的表面质量,且无毛刺,这是一家载客汽车气缸盖制造商最近的真实发现。该公司当时正在经历加工过程不稳定和毛刺问题,而另一个问题是刀片寿命不确定,主要原因是刀夹的调整位置在每次调整时略有差异。换用了M5B90刀具后,实现了流畅的精加工,且磨损情况可预测、无毛刺。该刀具仅产生非常薄的切屑,很容易在切削过程中去除,从而避免了对零件表面造成任何损害。此外,换用M5B90之后的刀具寿命从平均30,000个工件提升到了45,000个。
还可向客户提供CoroDrill®和CoroTap®系列钻削和攻丝刀具作为同系列汽车铝件加工解决方案的一部分,正如向客户提供标准的CoroMill® Century 590面铣精加工刀具一样。
无论何种情况,正如客户案例所示,有一点是切实存在的,那就是:确实能够缩短生产周期和降低单个零件成本,同时又能提升刀具寿命和质量。在汽车行业,因为大量生产司空见惯,所以哪怕生产周期的缩短非常有限,但是累积起来却能够成就巨大的经济回报。记住这一点,就很难忽略有能力创造可观回报的任何技术。